Polycrystalline solar panels have become a cornerstone technology in harnessing sustainable energy, and nowhere is this evolution more evident than in polycrystalline solar panel factories. These sites are not just industrial complexes; they are the beating heart of a global shift towards eco-friendly energy solutions. In this exploration of polycrystalline solar panel factories, we delve into the intricacies of the manufacturing process, uncovering the layers of expertise and meticulous precision that come together to produce these vital components of renewable energy infrastructure.
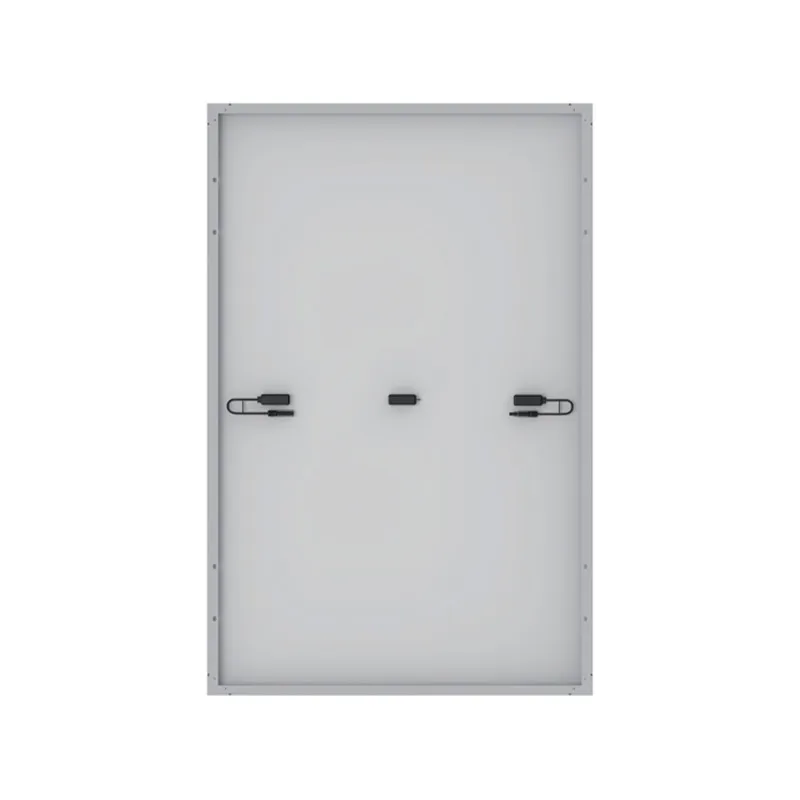
Polycrystalline solar panel factories are hubs of innovation and engineering prowess, embodying the synthesis of advanced technology and stringent quality controls. The journey begins with the raw material, silicon, which is abundant and forms the backbone of polycrystalline panels. Unlike monocrystalline panels that use a single crystal structure, polycrystalline panels utilize silicon fragments melted together. This difference results in a less energy-intensive manufacturing process, a crucial factor that makes these panels a widely preferred option for both manufacturers and consumers.
The manufacturing process starts with the melting of silicon, which is then poured into a mold to create ingots. These ingots are carefully cooled and subsequently sliced into thin wafers, employing an intricate wire saw technique that minimizes material wastage. This phase requires an astute understanding of material properties to ensure consistency and quality. Precision engineering at this stage is fundamental, as the efficiency of the solar cells directly depends on the texture and thickness of these wafers.
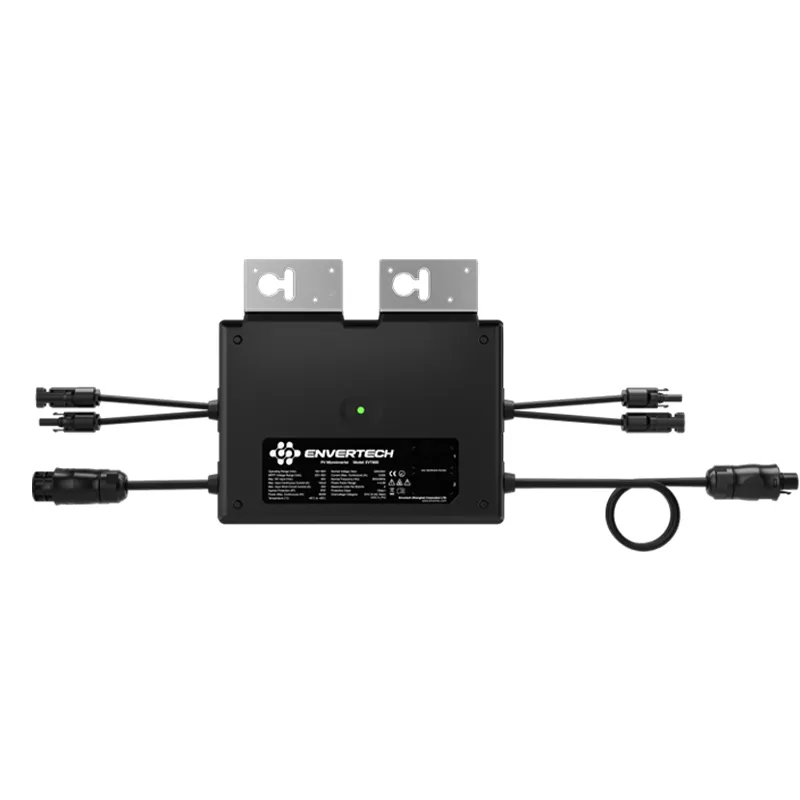
Once the wafers are formed, they undergo surface etching to enhance their ability to absorb sunlight. An anti-reflective coating is applied, reducing energy losses and thereby boosting the panel's efficiency. This is a critical step that demands expertise in chemical applications and the ability to control microscopic changes on the wafer's surface.
Assembly follows, where wafers are carefully aligned and interconnected, forming a complete solar cell. These cells are electrically conductive and can generate electricity when exposed to sunlight. At this point, the fabrication process transitions into a more delicate phase which involves the encapsulation of cells within protective layers. This structural integrity shield ensures durability against elements like moisture and extreme temperatures, thus extending the panel's lifecycle.
polycrystalline solar panel factory
Quality assurance plays a pivotal role throughout the production sequence at polycrystalline solar panel factories. Rigorous testing is conducted at various stages, with state-of-the-art diagnostic tools employed to evaluate efficiency metrics and operational consistency. These evaluations are not mere formalities but are essential to securing the factory's reputation as a reliable supplier of high-quality solar panels. Trustworthiness is built through a consistent demonstration of adherence to international standards and client expectations.
The expertise found within a polycrystalline solar panel factory extends beyond mere production. It includes a profound understanding of the photovoltaic market dynamics, supply chain management, and sustainable practices. This broad expertise contributes to the authoritative stature of these factories in the renewable energy sector. They are not just suppliers; they are pivotal players in the global transition to greener energy.
In addition to manufacturing prowess, these factories are often involved in pioneering research and development initiatives. Continuous innovation is essential for keeping pace with evolving energy needs and technological advancements. By investing in R&D, these factories reinforce their position as leaders in efficiency enhancement and cost reduction.
Ultimately, the reliability and efficiency of polycrystalline solar panel factories are the result of detailed craftsmanship and a commitment to quality. Each panel produced represents a step toward sustainable living and a reduction in carbon footprints globally. For end-users, the appeal of polycrystalline solar panels lies in their balance of affordability and performance, making them accessible solutions for residential and commercial applications alike.
In conclusion,
the significance of polycrystalline solar panel factories transcends their tangible outputs. They embody an intersection of skilled engineering, environmental stewardship, and economic pragmatism, contributing indispensably to a sustainable energy future. As the world increasingly turns to renewable energy sources, these factories stand as testament to what can be achieved when expertise and environmental responsibility are aligned.